In the ever-evolving landscape of metal fabrication, Superior Steel stands as a beacon of quality…
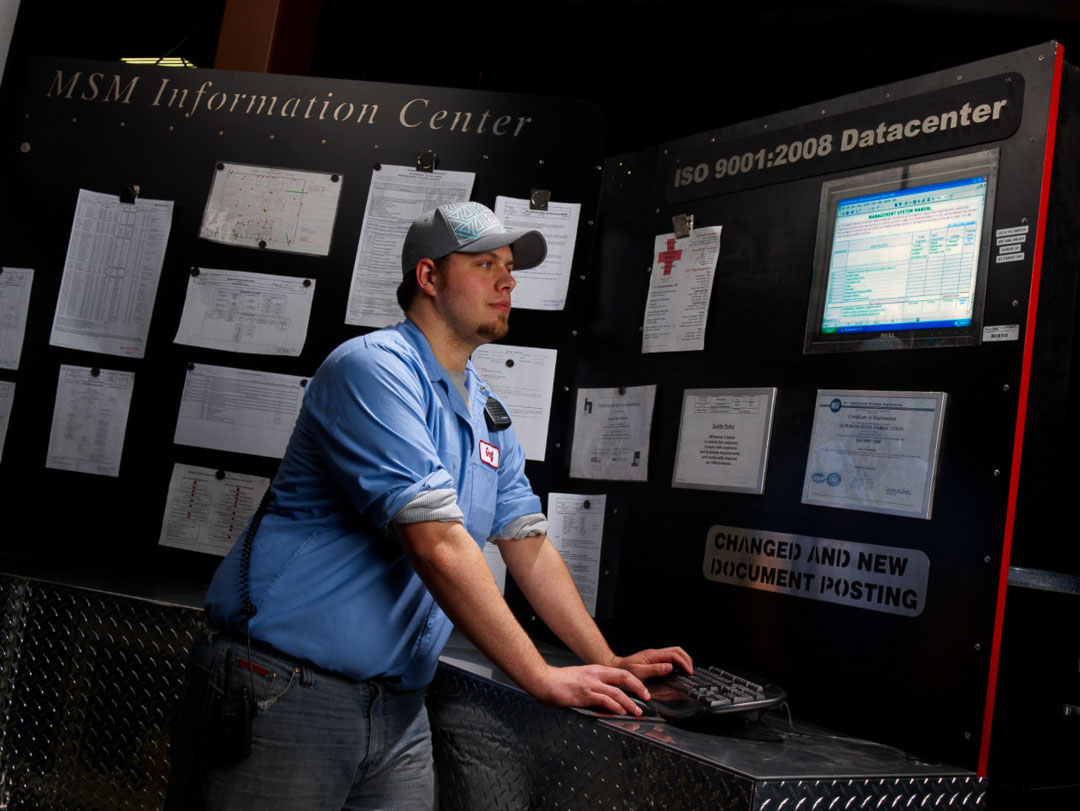
Inconel Machining: What You Need to Know
If you’re in the business of machining superalloys, you’ve likely come across Inconel. Inconel is a family of superalloys highly resistant to oxidation, corrosion, and scaling in high-temperature environments. Due to its unique properties, Inconel is a popular choice for aerospace, automotive, and chemical processing applications.
Machining Inconel, however, can be a challenge. In this blog post, we’ll take a closer look at Inconel machining and what you need to know to get the job done right.
What is Inconel?
Inconel is a family of nickel-chromium-based superalloys highly resistant to oxidation and corrosion at high temperatures. Inconel alloys exhibit excellent mechanical properties, including high tensile strength and fatigue resistance.
There are many different types of Inconel alloys, each with its own unique properties and characteristics. Some of the most common Inconel alloys include Inconel 600, Inconel 625, Inconel 718, and Inconel X-750.
Why is Inconel Machining a Challenge?
While Inconel alloys offer many benefits, they can also be difficult to machine. Some of the challenges associated with Inconel machining include:
- High Work Hardening Rate: Inconel alloys have a high work hardening rate, which means they become harder and stronger as they are worked. This can make it challenging to achieve the desired shape and size of the part.
- High Cutting Forces: Inconel alloys are difficult to cut, which can result in high cutting forces and tool wear.
- High Heat Generation: Inconel alloys generate a lot of heat during machining, leading to thermal damage and dimensional instability.
- Workpiece Deflection: Inconel alloys are prone to workpiece deflection during machining, which can result in dimensional inaccuracies.
Tips for Successful Inconel Machining
Despite the challenges, it is possible to machine Inconel successfully. Here are some tips to keep in mind:
- Use the Right Cutting Tools: Choose cutting tools designed specifically for machining Inconel. Carbide tools with a high positive rake angle are typically the best choice.
- Use Coolant: Inconel generates a lot of heat during machining, so it’s essential to use plenty of coolant to keep the temperature down and reduce thermal damage.
- Optimize Machining Parameters: Adjust machining parameters such as cutting speed, feed rate, and depth of cut to achieve the best possible results.
- Use a Rigid Setup: Inconel is prone to workpiece deflection, so it’s important to use a rigid setup to minimize deflection and ensure dimensional accuracy.
- Consider Post-Machining Operations: Inconel can be challenging to machine to the required tolerances, so it’s crucial to consider post-machining operations such as grinding and honing to achieve the desired accuracy.
Conclusion
Inconel is a family of superalloys that offer many benefits, including high resistance to oxidation and corrosion at high temperatures. However, machining Inconel can be a challenge due to its high work hardening rate, high cutting forces, and tendency to generate a lot of heat during machining. By using the right cutting tools, plenty of coolant, optimizing machining parameters, using a rigid setup, and considering post-machining operations, it is possible to machine Inconel successfully and achieve the desired results.