In an age where environmental consciousness is paramount, Superior Steel Fabrication is setting the benchmark…
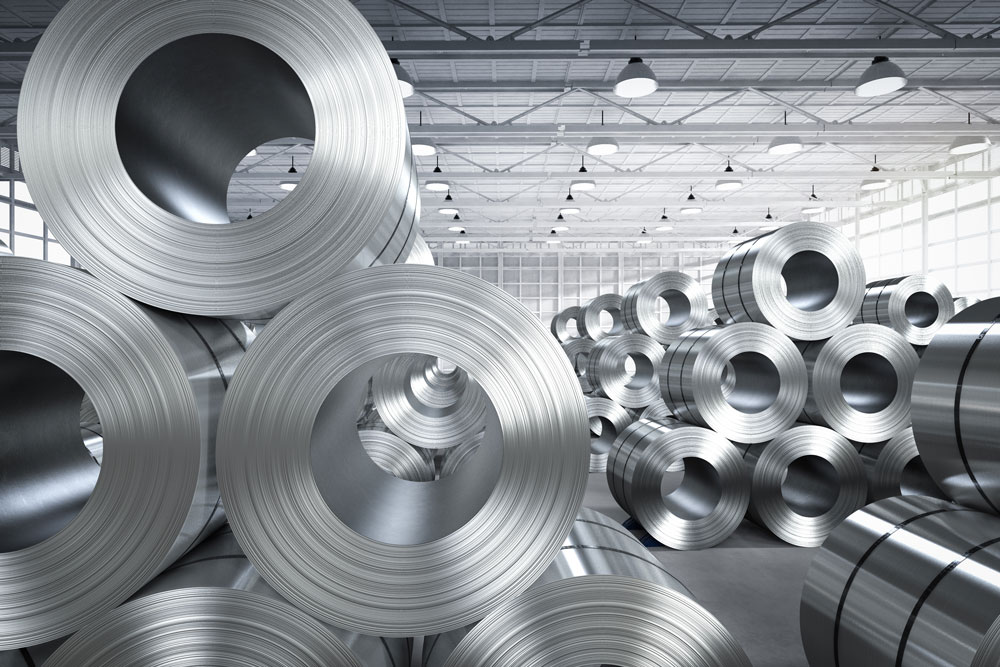
Steel vs. Aluminum: Making the Right Choice for Your Project
In the world of construction and fabrication, the choice of materials is pivotal. Steel and aluminum stand out as two remarkable candidates, each possessing distinct characteristics and advantages that cater to different project needs. Deciphering which material is best suited for a specific project involves a thorough understanding of their properties, uses, and the critical factors that should guide your decision.
Steel and aluminum, both exceptional in their own right, have carved a niche for themselves in various industries. Steel, renowned for its strength and durability, has been the backbone of colossal structures such as skyscrapers, bridges, and industrial frameworks. On the other hand, aluminum, celebrated for its lightweight and corrosion-resistant nature, has found its place in aerospace, automotive, and marine applications. As architects, engineers, and project managers consider which material to employ, several significant considerations come into play.
The Strength Factor
When it comes to strength, steel undoubtedly takes the lead. It’s hard to rival the sheer brute force that steel can endure. The robustness of steel makes it an ideal choice for projects that require load-bearing capabilities. Whether you’re constructing a high-rise building, a long-span bridge, or a heavy industrial complex, the structural integrity and resilience of steel come into play.
Aluminum, though lightweight and strong in its own right, doesn’t quite match the pure might of steel. It’s ideal for applications that benefit from reduced weight, such as aircraft and lightweight automobile components. Its high strength-to-weight ratio is perfect for situations where weight savings are crucial.
Weight: Steel’s Burden vs. Aluminum’s Blessing
Weight plays a pivotal role in many projects, especially those where mobility, transportation, or fuel efficiency are primary concerns. In such cases, aluminum shines. It’s about one-third the density of steel, which significantly reduces the overall weight of structures. For instance, in aerospace applications, a lighter frame translates into less fuel consumption, more efficient flight, and increased payload capacity.
In contrast, the heaviness of steel can be a limitation in certain scenarios. It demands substantial supporting structures and can be cumbersome to transport. However, in cases where the load-bearing capacity and rigidity are paramount, steel remains the superior choice.
Durability and Corrosion Resistance
One of aluminum’s most prominent attributes is its remarkable corrosion resistance. Unlike steel, which is susceptible to rust and corrosion, aluminum forms a thin oxide layer when exposed to the elements, which prevents further oxidation. This natural protection makes aluminum a superb choice for applications where exposure to moisture, salt, or acidic substances is common.
Steel, on the other hand, is inherently susceptible to corrosion. However, through the use of protective coatings, such as galvanization or painting, steel can achieve an impressive level of durability in harsh environments. The selection between aluminum and steel often depends on the intended application and the exposure to environmental factors.
Malleability and Formability
Aluminum is known for its exceptional malleability and formability. It can be easily shaped, bent, and formed, allowing for intricate designs and complex geometries. This quality makes it an attractive option for industries like automotive, where aerodynamic and aesthetically pleasing designs are essential.
Steel, while less malleable than aluminum, offers its own advantage in terms of formability. It can be fabricated into various shapes and profiles, making it suitable for a wide range of applications. Steel’s high tensile strength allows it to be stretched, bent, and manipulated to suit the desired specifications.
Cost Considerations
Economics play a crucial role in material selection for any project. Steel is often considered more cost-effective due to its abundance and established manufacturing processes. It’s readily available in various grades and shapes, making it a competitive choice for many applications. The abundance of steel also means it can be recycled efficiently, reducing raw material costs.
Aluminum, while still economically viable, tends to be pricier than steel. Its manufacturing process involves more complex and energy-intensive methods, contributing to its higher cost. However, its lightweight nature can offset some of the additional expenses by reducing transportation and installation costs.
Thermal Conductivity and Insulation
Aluminum’s high thermal conductivity makes it an excellent choice for applications where heat dissipation is essential. It’s commonly used in heat sinks and radiators in electronics, as well as in cookware due to its ability to heat quickly and evenly.
Steel, with its lower thermal conductivity, is less suitable for applications requiring rapid heat transfer. However, it’s an excellent choice when insulation from heat or electricity is needed. For example, in the construction of buildings, steel is often preferred because it doesn’t readily conduct heat or electricity.
Environmental Impact
The environmental impact of a material choice is an increasingly important factor. Both steel and aluminum have their merits and challenges in this regard. Aluminum is often regarded as more eco-friendly because it’s 100% recyclable with no loss in quality. Recycling aluminum consumes only about 5% of the energy required to create primary aluminum.
Steel is also highly recyclable, and much of the world’s steel supply is now produced from recycled materials. However, the recycling process consumes more energy compared to aluminum recycling. Nevertheless, advances in energy-efficient steel manufacturing are reducing its environmental footprint.
Choosing the Right Material
The choice between steel and aluminum ultimately comes down to the specific project requirements and priorities. When deciding, consider factors like:
- The structural demands of the project.
- Weight considerations, especially in mobile or transportation applications.
- The level of corrosion resistance required.
- Design complexity and aesthetics.
- Cost-effectiveness.
- Thermal properties and insulation needs.
- Environmental impact and sustainability goals.
It’s also worth noting that hybrid solutions often combine the strengths of both materials, catering to diverse project needs.
When you have questions, Superior Steel Fabrication has the answers. Contact us today!