A near-endless amount of new sheet metal fabrication applications are being developed every year. By…
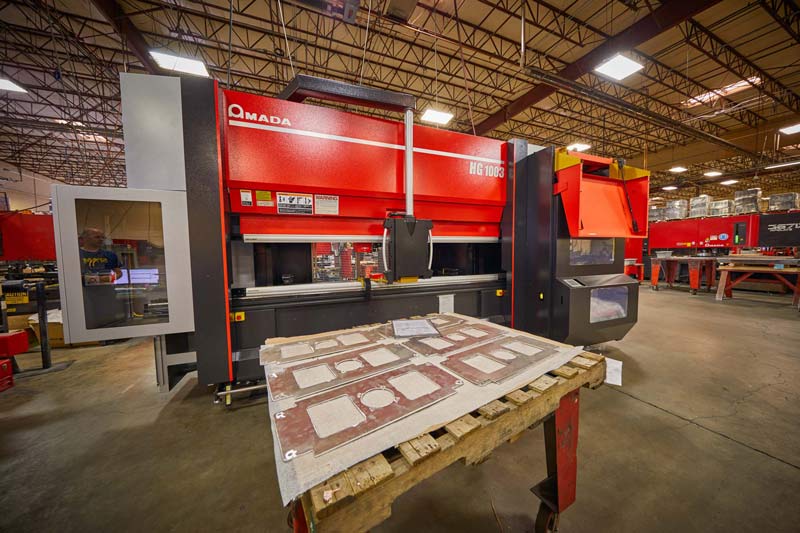
Sheet Metal Fabrication Techniques
Sheet metal can be bent, curled, punched, stamped, spun, cut, welded, or stretched to form the desired shape and structure of its manufacturer. This high level of versatility makes sheet metal a go-to material across a wide variety of industries which require some sort of customized fabrication.
Superior Steel Fabrication is here to go over the basic techniques of sheet metal fabrication.
Sheet Metal Fabrication Techniques
Bending Metal
A process done by hammering or with press brakes
Form Bending – This is the simplest way to bend metal. In this method, you are bending the metal over an edge or shape. You could also use a hammer and shaping dolly to bend the metal around the shape that is desired.
Metal Brake – A metal brake is the most common way to make clean, precise bends in metal. A metal brake works by placing the metal on a flat, gated surface and then clamping a flat bar on top of the metal and lifting the gated portion to bend the metal to the desired angle. Most metal brakes can make bends to just over 90 degrees. We offer a selection of diverse sheet metal brakes on our site.
Cutting Metal
Hand Shears – The most basic and fundamental metal cutting tool in the world of metal fabrication.
Power Shears – Allow you to cute sheet metal quicker and with less manual effort than hand shears. Power shears come in many forms, including pneumatic and electric shears. Most are not capable of cutting around tight corners or complex shapes and will usually waste material.
Throatless Shears – These are designed to allow you to cut metal in straight lines or shapes without marring edges. Throatless shears are operated by hand and do not waste material.
Angle Grinder – An electric angle grinder is a handheld tool that spins an attached disc or wheel to cut metal. For cutting, the 0.045-inch-thick wheels should be used which can pretty much cut through any thickness of steel. They are loud and messy but get the job done.
Plasma Cutters – Plasma cutters work by sending an electric arc through a gas that is passing through a constricted opening. This elevates the temperature of the gas to the point that it enters the fourth state of matter: plasma. Plasma cutters can cut sheet metal quickly while still maintaining a high level of accuracy. They can be as powerful or delicate as you want. They are great for making long straight cuts and require very little cleanup.
Stretching Metal
Hammer and Dolly – The most basic way to stretch metal where an object is held behind the metal and the other side is hit with a hammer.
Stretcher – This is a mechanically operated tool that puts the metal between two flat textured jaws and pulls the metal apart slowly each time the lever or foot pedal is pressed.
English Wheel – Also called a wheeling machine, stretches the metal between a top rolling wheel and the bottom anvil wheel. English Wheels are commonly used to fabricate coach-built automotive panels, aircraft skins, and more.
Shrinking Metal
Tucking – Tucking metal is one of the earliest methods of shrinking metal which involves bunches the metal with a hammer and form.
Shrinker – Textured jaws gasp sheet metal from top and bottom and force it together tightly. This method is slower that tucking, but much more precise and leaves minimal marring.
Heat Shrinking – This method takes a lot of practice and consists of a fabricator heating an area that is overstretched with a torch which then shrinks when it cools.
Metal Fusion
The most common type of metal fusion is welding.
Oxy-Fuel Welding – The oldest welding method that uses welding uses oxygen and acetylene that are mixed together with an adjustable torch to create a precise, controlled flame. This method takes a lot of practice to master, but the welds produced are the softest and most pliable making them easiest to smooth out.
TIG Welding – Uses a “torch” that has a non-consumable electrode that creates a small, precise electric arc that melts the base metal. TIG welds are the second softest weld but are the most difficult to master. TIG welding is more precise than oxy-fuel welding and preferred by most modern, professional fabricators.
MIG Welding – The most common and probably the easiest form of welding to learn. This method uses a motor to feed the filler wire through the tip of the MIG gun. The wire then completes the circuit when it touches the base metal and melts the wire into the weld joint, fusing the metal together. MIG welding creates sparks and requires more cleanup than the other methods above. It’s also the hardest weld, so it’s harder to grind and hammer flat.
When you’re looking for a company to fabricate a large sheet metal project, you want to be assured that your work will be completed with a high degree of craftsmanship.
No matter the project, Superior Steel Fabrication will work with you to make sure your sheet metal goals are met in a timely, professional manner with exceptional results.
Contact Superior Steel Fabrication today or give us a call at (541) 242-6420 to discuss the details of your project and request a quote. We look forward to working with you.